Packaging is the first point of contact between consumers and brands, and it is also the way for consumers to directly obtain product information and brand information. Beautiful coffee packaging bags can give customers a profound first impression of your brand through visual impact, thereby significantly increasing the probability of repurchase behavior.
Therefore, customized exclusive coffee packaging bags have become essential for marketing brands. In order to clearly display the text, pictures, logo, and other information, it is also vital to choose the corresponding printing technology that matches the packaging material.

Based on our years of experience in the production of packaging bags, we recommend three commonly used printing processes here, namely: flexographic printing, gravure printing, and digital printing.
What is flexographic printing?
Flexo printing is a type of letterpress printing using flexographic plate technology. Ink is applied to various surfaces using flexible rubber (or other elastomeric) printing plates. The inks used in flexography dry quickly by evaporation and are safe for use on wrappers that come into contact with food. However, only one color can be printed with each flexographic plate.
The printing accuracy of flexo printing is high. The color saturation is strong, and the printing speed is relatively fast. Since each color requires a different plate, the setup is complicated, making it poorly suited for small jobs requiring a quick turnaround.
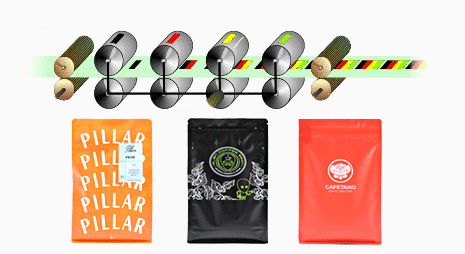
What is gravure printing?
Gravure printing is one of the four printing methods. It uses a printing plate composed of pits corresponding to the original design. The pits are filled with ink during printing, while a squeegee removes any excess ink that is not part of the design. Next, pressure is added between the printing plate and the substrate helps transfer the image to the substrate, completing the printing. Gravure printing, like flexo printing, can only print one color per plate.
Gravure printing has become one of the most important printing processes for manufacturing customized packaging due to its relatively low cost, thick ink layers, bright colors, higher accuracy, stable printed product quality, and fast printing speed.
However, the production cycle is also longer since each color requires a printing plate, which is complicated to make.
What is digital printing?
Although digital printing is relatively new, it has developed rapidly. Unlike traditional methods, digital printing does not require special plates that take additional time to produce. Designs are immediately transferred from the design draft on a computer. If there are multiple packaging designs of the same size, they can also be printed simultaneously. However, in the traditional printing process, plates need to be re-made regardless of whether the size is the same when the designs are slightly different, costing merchants more time.
There are many types of inks that can be used in digital printing. In addition to the water-based inks that have always maintained their advantages, there are also more ecological inks and UV inks. Therefore, digital printing is more environmentally friendly than traditional printing processes and more aligned with modern environmental protection concepts.

With a clear understanding of the principles and main advantages and disadvantages of various printing processes, which printing process is most suitable for your customized coffee packaging needs? Based on years of experience with multiple orders, we have summarized the suitability of each process below:
1. Flexographic printing:
We have learned before that flexographic printing can only produce one color at a time, which means printing plates must be made ahead of time. Although the printing speed is fast, the preparation work is complicated, rendering a longer production cycle than other methods. Therefore, flexographic printing has high order quantity requirements. On the upside, the ink used in flexographic printing is not easy to smudge and can be directly printed on kraft paper bags. If your order for customized coffee bags is in high demand and you want to print directly on compostable kraft paper, we recommend you use flexographic printing.
2. Gravure printing:
Some readers may find that there is little difference between gravure printing and flexographic printing. Both need extensive preparation, creating longer production cycles due to the nature of one-time-use printing plates. However, gravure printing has other advantages that flexo printing does not: first, the price. Although plate making is required, gravure is relatively cheap. The second is the ink. Thanks to the ink-filled pits used in this method, the packaging has a solid ink layer, bright colors, and rich layers.
These advantages make gravure printing superior to flexographic printing. So if your order is large, gravure printing is the most cost-effective and most suitable printing method. However, flexo printing is best if you want to print your design directly onto kraft paper.
3. Digital printing:
Digital printing can achieve what the traditional printing process cannot: simultaneously printing different designs of the same size. The biggest advantage of digital printing is that there is no need to make plates in advance, and it has strong pressing capabilities. The production efficiency of digital printing is higher, the production cycle is shorter, and the MOQ can be as low as 500.
If you are a small or medium-sized seller and attach great importance to the flexibility of the turnaround, digital printing is your best choice.
If you want to launch a limited short-term plan, digital printing is your best choice.
If your product is multi-SKU and the quantity of each item is small, then digital printing is more suitable.
If you want to be more environmentally friendly, digital printing is the most ecological option.
Now that we’ve gone over the printing processes, you may be curious about the machines that do all the work. This section will introduce two of the most commonly used printing machines: gravure printers and digital printers, using the machines in our factories as an example.
1. Gravure printing machine.
The more common machines are 9-color and 10-color gravure printing machines. Since our factory does not have a 9-color printing machine, we will discuss the 10-color variant. As the name suggests, the 10-color gravure printing press can produce more colors. The coffee bags made by the factory with the gravure printing machine are in strict accordance with the requirements of the Pantone color card, so you can choose the gravure printing process with the utmost confidence. We can accept a MOQ of 2000.
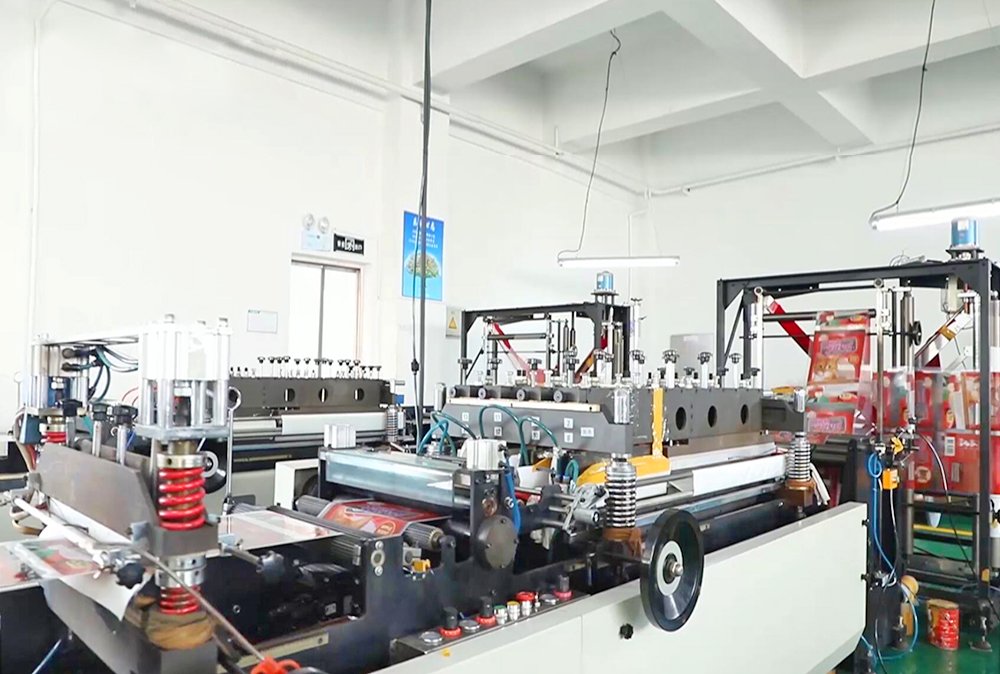
2. Digital printing machine.
Digital printing machines on the market have been consistently updated. We bought the HP Indigo 20000 and HP Indigo 25000 when they first came out. In color mode, the printing speed is 42 meters per minute. It supports 7-color printing and can meet the vast majority of design needs.
Supporting a wide variety of substrates, the 29-inch image width can handle most flexible packaging and pressure-sensitive labels, making printing more efficient. With seven ink stations and a color gamut of up to 97% of PANTONE® colors, the converter can meet stringent brand color needs. To provide more user-friendly solutions for your custom packaging business, we can now accept a MOQ of 500.

With an understanding of popular packaging and printing processes, you can choose the most suitable printing method according to your needs. If you still have questions about the printing process, feel free to contact us, and we will be happy to have a more in-depth discussion with you.